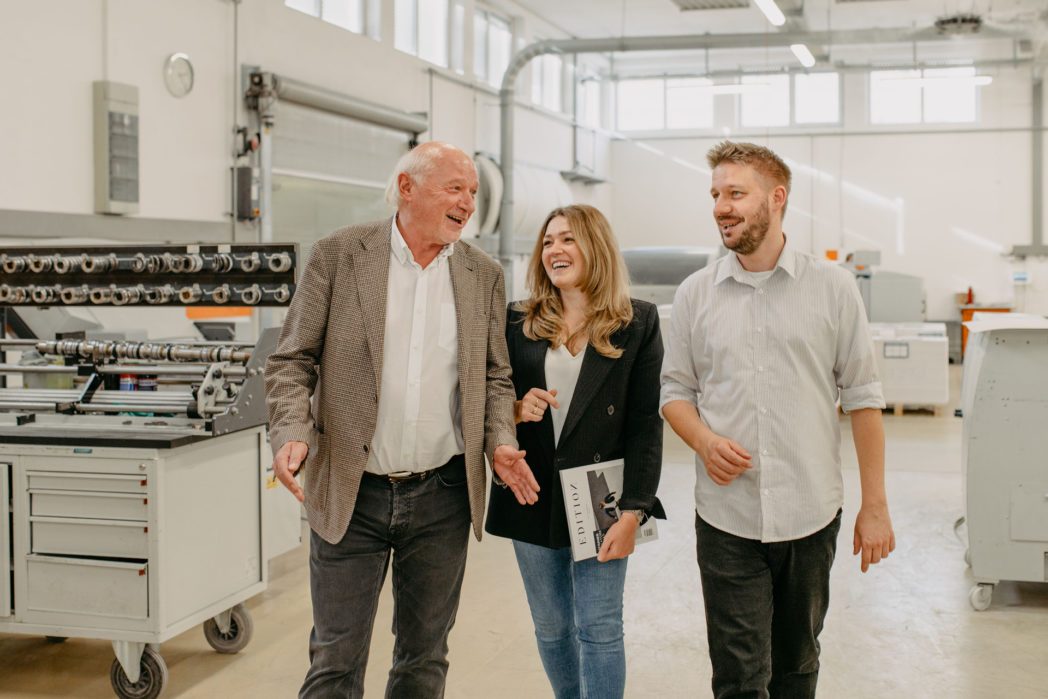
Just as products, raw materials, materials and printing techniques move with the times, the organisational structure of a company must also be updated. This is why the printing house Samson Druck decided to restructure its internal processes and clearly distribute areas of responsibility as part of the upcoming generational change in many key positions. “We are a family business with many young but also some long-standing employees in key positions. My uncle Gerhard Aichhorn has been running Samson Druck for over 40 years and has led the company to success. Some of our most experienced employees have been with the company for a similar length of time and will be retiring in the foreseeable future or have recently retired. They all have a wealth of experience. As the next generation, my cousin, Lisa Frost, and I see it as the aim of the project to retain this valuable wealth of experience and transfer it to the next generation. At the same time, we want to combine this experience with the skills of our many young employees,” says Markus Ramsbacher.
Working together on the future
The challenge in restructuring the company is therefore not just the transfer of knowledge. Employees with experience and expertise should also be able to develop in the operational business in order to be involved in strategic processes and decision-making. “I have previously worked in other companies and have seen how the management structure is supplemented by an ‘expert council’ and how it works well. As part of our project, we are training employees in this regard and forming a management circle that reflects the experience and expertise of all relevant areas. In this way, we can ensure that we make the best possible decisions together in the future,” says Markus Ramsbacher. “We have brought in external help for this. We are working with a consultant to work out what happens in the individual departments, what role which employees have, where their tasks and responsibilities lie, as well as tips and tricks. We also want to find out how the team assesses individual operational and strategic issues and what adjustments we can make as a result. This is the structural side of the project. We are working with a second consultant on the upskilling of our team. We want to empower our team leaders to lead their teams not only operationally, but also strategically.”
Digitalisation is also part of this
Another part of the project is the switch to the use of modern, digital tools. All work steps and orders are embedded in quality management software. This will make all processes transparent and traceable for everyone: What is the work step, who authorised the process, who checked it? These and other parameters contribute to quality assurance. This also means that all employees always have the same level of knowledge. This avoids ambiguities. “We want to maintain our ability to make decisions quickly and at short notice, which is the strength of an SME,” says Markus Ramsbacher.
The work areas have been equipped with tablets on which the software runs. Maintenance and cleaning schedules for individual systems are also stored there, for example, in order to organise these processes in a low-threshold manner. “I trained employees who were afraid of digital technology on the tablets,” says the junior manager. “But we were able to dispel these fears by listening to their needs and making it as easy to use as WhatsApp, which pretty much everyone can use. And that worked well. Today, operating the tablets is no longer an issue.”
The print shop is currently in the middle of a project for which it was able to apply for the “Arbeitswelt 4.0” funding programme. This funding can be applied for New Work, digitalisation, lifelong learning and similar processes. Samson Druck was supported by Ulrike Klingenschmid and Florian Dürager from our Innovation Service Centre.
About Samson Druck GmbH
- Family business
- Margarethen in Lungau
- 120 employees
- Offset printing company
- samsondruck.at
This might also interest you
10. July 2024
Funding for film, TV, and streaming projects
Austria offers national and regional funding for film projects. Funding is available for international service productions, Austrian cinema films, and emerging productions. This covers cinema, TV, and streaming. The largest component of this is the incentive model FISA+.
5. June 2024
The Faculty of Digital and Analytical Sciences after 2 years – a review
Since its establishment two years ago, the Faculty at the Paris Lodron University of Salzburg has seen significant expansion. This was also supported by the State of Salzburg and Innovation Salzburg. On Tuesday, June 4, 2024, a review was presented at a press conference.
17. January 2024
Research premium – this is how you apply!
SMEs can apply to the tax office for a research premium for expenditure on research and development (R&D). We show you how it works!
23. November 2023
Digital Motion: Enhancing Movement with Technology
Several research institutions in Salzburg, along with additional partners, have succeeded in bringing another COMET project to Salzburg with “Digital Motion.” COMET is the flagship program for promoting cutting-edge research in Austria.