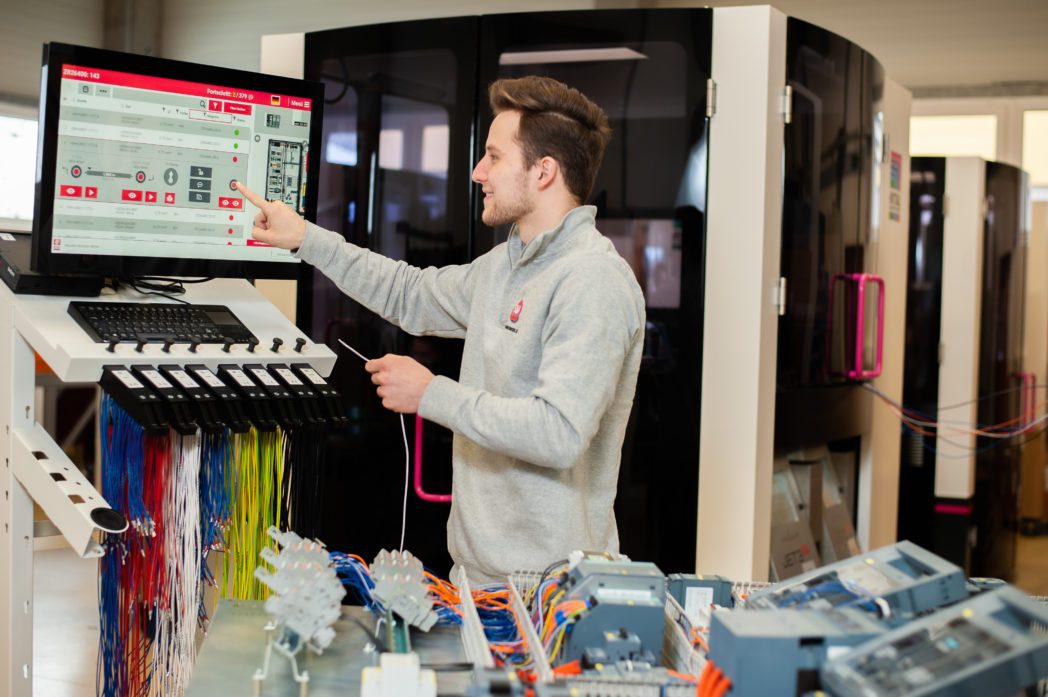
SW Automation has been manufacturing custom control cabinets for special-purpose machines for nearly fifty years. The manufacturing processes of a control cabinet have undergone fundamental changes during this time, as the Golling-based company is now fully digitized.
SW Automation’s services range from planning and programming to the production of control cabinets. This includes electrical circuit planning, planning of electrical safety, and programming for control systems. This ensures that the machine controlled by the control cabinet does what it is intended to do. Another aspect of machine automation is the programming of various drive technologies, utilizing both servo motors and robots. IT connections ensure that different ERP systems are linked to the machine control.
From Wire to Control Cabinet
The control cabinets are manufactured in the in-house workshop, where the individual components are wired together. In the past, the control cabinets were manually wired based on electrical circuit diagrams, a time-consuming and labor-intensive process. That’s why SW Automation wanted to automate their own processes for control cabinet production. In 2005, they began using CAD programs to calculate the wires within a control cabinet, which were then produced by an external wire harness manufacturer. However, the wiring still relied on manual labor, making rapid changes difficult, and increased demands for delivery times made external procurement no longer feasible.
The Wire Harness Machine
In 2014, the company decided to take the next step in digitalization, automating not only for its customers but also for itself. With the support of an FFG basic funding, the wire harness machine was developed. With this innovative novelty in the market, the company can produce 36 different wires for their control cabinets without any manual intervention. This has given the company a significant competitive advantage. “Initially, we developed the wire harness machine for our own production of control cabinets. It was only in 2016 that we decided to turn it into a marketable product, as we recognized the potential of our machine,” says Felix Grünwald, CEO of SW Automation.
The Digital Twin as the Basis for Control Cabinet Manufacturing
But it’s not just wire production that has been digitized; the entire process of control cabinet manufacturing is now digitalized. The control cabinet is represented in a virtual 3D model using the digital twin. “The digital twin is the basis for everything we do in our company, allowing us to create a continuous digital process,” explains Felix Grünwald. The information from the digital twin is transmitted to the wire harness machine. The machine produces the wires for the control cabinet with the desired parameters, such as length or labeling, and arranges them in the correct order for installation. The wiring of the cables in the control cabinet by the electrical technician is done at the digital wiring workstation, where a wiring app provides instructions for proper connection. The cable routing is documented and fed back to engineering, completing the digital circle of control cabinet wiring.
The Future of the Wire Harness Machine
The machine is now being produced in series. However, this is by no means the end of the possible applications and further development of SW Automation. “We have many ideas and projects for the future in the field of wire harnessing,” says Felix Grünwald.
This might also interest you
6. March 2025
salz21: Necessary Steps for the Future
On March 5, 2025, salz21 | Home of Innovation once again provided a platform for future topics, innovations, and interdisciplinary exchange. More than 1,000 visitors took the opportunity to learn about current developments and discuss perspectives for tomorrow. Three topics were particularly dominant: climate protection, artificial intelligence, and a strong Europe.
25. September 2024
Green Deal: How Sustainable Business Development Can Look
The EU aims to create political and legal frameworks through the Green Deal to transform both the economy and society in a sustainable way. The Pinzgau-based company Design Composite demonstrates how this can be implemented.
15. August 2024
Sunbeam Yachts: Where Craftsmanship Meets Digitalization
Sunbeam Yachts has been building exclusive sailing yachts at Mattsee for generations. The production is done by hand, with some processes now digitally supported.
12. August 2024
SBS: One Software for Many Self-Service Devices
As a leading provider of banking software in Salzburg, SBS is now exploring new markets. The company remains true to its core segment by offering manufacturer-neutral software for self-service devices in additional sectors.